This digest reflects the current status of Russia’s MC-21 narrowbody aircraft program, highlighting the comprehensive effort to achieve technological independence while meeting domestic market demands. The program represents a significant milestone in Russian commercial aviation development, with substantial implications for the country’s position in the global aerospace market.
Russia’s comprehensive domestic aviation industry development program targets the production of 270 MC-21-310 aircraft by the end of 2030. The program schedules delivery of nine aircraft to customers in 2025, though deliveries will not commence before mid-fall of the following year. Certification flights began in June and are expected to continue through September 2026, according to Yakovlev Design Bureau officials. Production volumes are projected to reach 72 MC-21 aircraft annually by 2029-2030.
While these production targets are ambitious, ongoing certification delays for the import-substituted variant and the dynamic economic and technological environment may necessitate schedule adjustments. The Irkutsk Aviation Plant (IAP) has stated that current manufacturing capacity limits annual MC-21 production to 36 aircraft.
Aeroflot Orders and Fleet Integration
Aeroflot, Russia’s flag carrier, ranks among the first customers for the new aircraft and plans to begin MC-21 operations in Q4 2026. CEO Sergey Aleksandrovsky confirmed these timelines in an interview with journalist Pavel Zarubin on Russia 24 television channel. He noted that United Aircraft Corporation (UAC) has confirmed the delivery schedule, providing Aeroflot with confidence in fleet integration planning.
“Our objective is incorporating new domestic MC-21 aircraft into the group’s fleet. We plan to receive more than 100 aircraft by 2030, and preparation for operations is already underway,” stated the Aeroflot CEO. The airline group’s post-2030 development strategy encompasses delivery of 339 domestic aircraft, including 210 MC-21s, 89 SJ-100s (Sukhoi SuperJets), and 40 Tu-214s.
Aeroflot pilots have expressed interest in MC-21 type rating training, indicating positive reception of the new aircraft and readiness for operational transition. Training utilizes advanced simulators developed under contract with Yakovlev PAO. Concurrent technical specialist training includes theoretical and practical preparation with mandatory certification. This comprehensive approach will ensure reliable operations and minimize downtime when introducing new aircraft into the carrier’s route network.
Lightning Protection Testing
Ground testing continues at Yakovlev PAO’s Flight Test and Development Complex at Ramenskoye Airport in Zhukovsky, focusing on prototype aircraft MC-21 with tail number 73051. Engineers from the test complex, working with specialists from Gromov Flight Research Institute, are evaluating the MC-21’s lightning strike protection systems. These tests form part of the import-substituted variant’s certification program, with electrical current simulating lightning strikes applied to the aircraft fuselage.
The primary objective involves measuring induced voltages in onboard cable networks and verifying lightning protection for aircraft systems to identify and eliminate potential vulnerabilities in electrical systems. Testing simulates probable lightning strike points by applying current pulses up to 5 kA and voltages up to 10 kV, enabling assessment of atmospheric electrical discharge protection effectiveness.
Aircraft 73051 represents the first MC-21 prototype that underwent complete cable network replacement during 2022-2023 as part of import substitution and re-engining with PD-14 engines (a Russian-developed turbofan). Ground lightning protection testing must confirm aircraft safety and reliability during operations in adverse weather conditions and constitutes a certification documentation requirement.
Market Demand and Production Capacity
Russian airlines are prepared to contract for 200 MC-21 aircraft deliveries, according to Transport Minister Roman Starovoyt. This statement was made during an interview with Izvestia newspaper at the St. Petersburg International Economic Forum. The minister emphasized domestic carriers’ interest in fleet renewal with new Russian aircraft.
Starovoyt noted that creating a new aircraft fleet represents a lengthy and comprehensive process encompassing not only prototype development and production but also thorough certification work. He emphasized that certification directly relates to aircraft operational safety and represents a lengthy, comprehensive process involving meticulous documentation development and numerous testing procedures.
Manufacturing Facility Modernization
The Irkutsk Aviation Plant continues technical re-equipment of mechanical assembly production to increase MC-21 serial aircraft output rates. Preparatory work for new machine tool installation proceeds simultaneously across multiple shop floor areas.
In Shop 232, at the former cutting section location, facilities are being prepared for nine machining centers that will supplement the equipment fleet in Shops 201, 217, and 269 for titanium component manufacturing. Irkut-Remstroy currently performs this work, with Energotsentr-Irkut specialists soon joining to install pneumatic and electrical systems.
Shop 221 utilizes specialized equipment to prepare foundations for two multifunctional milling centers designed for aluminum alloy processing. Construction work in Shop 269 will begin shortly, equipping it with new Belarusian-manufactured machine tools. These measures aim to enhance production capacity and technological capabilities.
Investment and Modernization Program
The aviation plant received approval from the Irkutsk Regional Investment Council for a technical re-equipment project exceeding 65 billion rubles (approximately $650 million). The modernization objective involves launching MC-21 serial production and achieving 36 aircraft annual assembly rates by 2027. Plans include constructing new facilities, reconstructing existing shops, implementing modern equipment, and recruiting and training highly qualified specialists. Program implementation extends through 2030 with phased enhancement of production infrastructure and technological foundation.
IAP’s modernization encompasses construction of new production facilities and expansion of core manufacturing capabilities including forming/stamping, mechanical assembly, unit assembly, and final assembly/testing. The first re-equipment phase is complete with new production lines installed, galvanic production modernization continuing, and site preparation for advanced equipment ongoing. This comprehensive renewal will enable the plant to achieve planned output levels and ensure import-substituted system production for the MC-21.
Regional authorities support project implementation, assuming responsibility for creating favorable investor conditions and developing social infrastructure. IAP modernization is considered strategically important for Irkutsk Regional industrial development and the broader Russian aviation industry. The project is expected to increase new aircraft production volumes, expand employment, and strengthen domestic aviation industry positions in both domestic and international markets.
Cost Competitiveness Strategy
United Aircraft Corporation CEO Vadim Badekha told RBC that achieving cost-effective aircraft pricing comparable to foreign competitors represents a primary import substitution objective. He noted that immediate achievement proves challenging since initial production batches cost more due to low production volumes, high interest rates, and substantial investments in new systems and components.
According to Badekha, cost reduction programs have been developed for MC-21 and SJ-100 aircraft, with major implementation phases scheduled for completion by 2030. He emphasized this as a large-scale, complex task that the corporation considers key, since successful market entry requires competitively priced aircraft.
The UAC executive also reported ongoing negotiations with airlines including Aeroflot, as well as the Transport Ministry and Federal Air Transport Agency, to align aircraft commercial efficiency parameters with operator business models and maximize requirement compliance.
Interior Systems Integration
The Irkutsk Aviation Plant completed preliminary installation of Russian-manufactured interior systems on MC-21 prototype aircraft (tail number 73057). The aircraft received overhead bins, window and ceiling panels, galley and lavatory modules, and business-class seats. Aviation Interiors manufactured these components under the import substitution program.
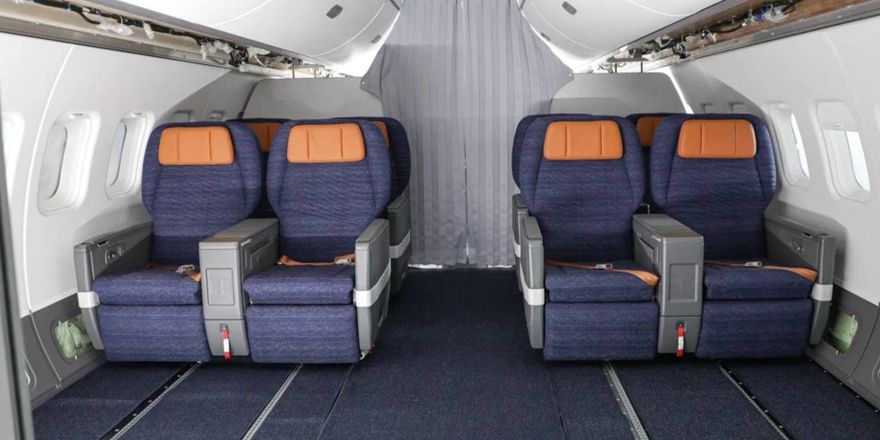
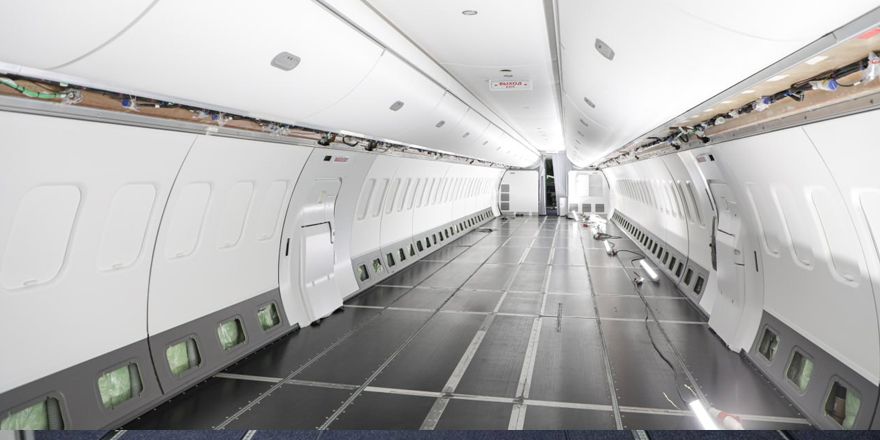
Genar Shuvalov, head of interior department at Yakovlev PAO, noted the high quality of Russian components that fit precisely during installation. Roman Ramazanov, CEO of Aviation Interiors, announced the launch of serial MC-21 interior production. The company plans complete import substitution of floor panels and overhead compartments with production facilities in Ulyanovsk.
Certification Flight Testing
In early June at the Zhukovsky test complex, MC-21 prototype aircraft with tail number 73055 underwent comprehensive system checks and calibration in preparation for certification testing. Yakovlev engineers and test pilots, working with the design bureau, provided technical support and aircraft condition monitoring throughout all preparation phases.
On June 26, 2025, following completion of factory development testing, aircraft 73055 performed its first flight under the supplemental certification testing (SCT) program. The flight evaluated radio communication equipment performance, including signal quality and communication range.
Rostec Executive Director Oleg Evtushenko noted that work proceeds under tight schedules since airlines await MC-21 aircraft deliveries. More than 20 aircraft in various completion stages are currently at the factory, with new aircraft deliveries to customers planned for next year. MC-21 Chief Designer Vitaly Naryshkin confirmed that approximately 220-230 test flights are required to ensure complete passenger safety.
During June, two prototype aircraft – 73054 and 73055 – completed seven flights totaling more than 25 hours. Aircraft 73054 conducted flights evaluating the import-substituted Traffic Collision Avoidance System (TCAS), while 73055 performed factory development and supplemental certification flights.
Testing Program Scope
The SCT program will utilize two prototype aircraft – 73055 and 73057. Aircraft 73055 will undergo certification of radio communication equipment, fire protection systems, and flight/navigation systems. Aircraft 73057 will certify fuel systems, hydraulic systems, anti-icing systems, and other aircraft equipment. Natural icing condition testing will occur in Arkhangelsk, while shimmy effect testing will take place in Ulyanovsk.
Aircraft 73055 features Russian radio-electronic equipment, auxiliary power unit, air conditioning and pressurization systems, domestic lighting, control panels, electrical power system, hydraulic systems, and landing gear. Only three non-critical imported components remain – actuators, brakes, and generators, which will be replaced with Russian equivalents on prototype aircraft 73057 and subsequent production aircraft. Resumption of fully import-substituted aircraft 73057 flights is expected within 1-2 months.