The first flight of the import-substituted MC-21-310 with the tail number 73055 was the key event of the month. The aircraft took to the skies on 29 April from the airfield of the Irkutsk Aviation Plant. The crew, consisting of the commander, test pilot, and director of flight testing at PJSC “Yakovlev” Roman Taskaev, test pilot of PJSC “Yakovlev” Alexander Guskov, as well as lead engineers for flight testing at PJSC “Yakovlev” Alexander Popov and Alexander Solovyev, spent 1 hour and 15 minutes in the air. The flight was conducted at altitudes of up to 3,000 metres, reaching a speed of 580 km/h. During its first flight, the MC-21 was accompanied by the Yak-130, from which filming was conducted. The Yak-130 was piloted by test pilot of PJSC “Yakovlev” and Hero of Russia Oleg Mutovin, while the filming was handled by test pilot of the Irkutsk Aviation Plant Dmitry Denisov.
During the flight, the MC-21-310 crew tested the functionality of the domestically produced avionics, electrical systems, air conditioning, and several other systems. After completing the factory refinement tests, the aircraft will return to Zhukovsky for certification testing.
At the Gagarin Komsomolsk-on-Amur Aviation Plant (KnAAZ), press equipment is being modernised to accelerate the production of skins for the MC-21. Previously, these components were manufactured in Ulyanovsk at the “Aviastar” plant, but production has now been relocated to the Far East. Each skin requires an individual approach during the setup of the new production line. Such work is rare and typically occurs during the launch of new models. The last time this was done was eight years ago during the creation of the “Superjet.”
The challenge in mastering the forming process for the MC-21 skins lay in the fact that KnAAZ and “Aviastar” use different presses. As a result, the tooling transferred from “Aviastar” was unsuitable. Engineer Anton Krivenok found solutions for manufacturing the skins, but they were not optimal. Due to this and the tight schedule, a contract was signed with the engineering company “ITS,” whose specialists prepared programs for six skins and proposed improvements to the forming technology.
The relocation of skin production to KnAAZ is part of the strategy to increase the production rate of the MC-21. It also allows for the utilisation of the production capacity of the plant in Komsomolsk-on-Amur, which is one of the key enterprises in the Russian aviation industry.
* * *
At the Irkutsk Aviation Plant, the modernisation of the machine park for the serial production of the MC-21 continues. The plant plans to produce 36 MC-21 aircraft per year. In recent years, a large-scale technical modernisation program has been implemented to improve production efficiency and meet the government-mandated production rates for the MC-21. The plant has already replaced outdated equipment, reconstructed workshops, and introduced modern technologies.
Specialists in Workshop 227 are completing the connection and commissioning of newly received machines equipped with an indexing chuck, which allows the workpiece to be rotated by 45 or 90 degrees. This simplifies the production of complex fittings such as tees, elbows, and crosses. Now, such components can be produced in a single setup, reducing manufacturing time. The old turret lathes have been dismantled.
Additionally, five “Proton T250” machines from the Perm-based plant JSC “STP PZMC” have been installed in Workshops 226 and 227. They are already operational, while another 11 units are undergoing commissioning. The main equipment needs for the serial production of the MC-21 in these workshops have been met.
In Workshop 246, the assembly of the 24th set of MC-21 semi-fuselages has begun in the new PF20 and PF30 stations. These stations will be used to assemble the fairing and prepare it for joining in the F05 station. The new stations for Workshop 246 were manufactured and assembled at IAZ by specialists from Workshop 218 and “Irkut-StankoService.” The PF20 station is designed for working with the forward semi-fuselage, while the PF30 is for the aft semi-fuselage. The upper part of the stations includes an area for storing templates of passenger floor panels.
Before assembly, the PF20 and PF30 stations were tested using special weights. The semi-fuselages were then carefully removed from the supports by crane and transferred to two synchronised trolleys. These trolleys transported the semi-fuselages to the station area, where they were placed on positioners.
Positioning is carried out using software that accounts for even the slightest load variations on the positioners and prevents incorrect installation of the assembly via rigging nodes. In the new stations, detailed assembly of the walls and diaphragms will be performed on the semi-fuselages, followed by the installation of the assembled walls onto the fuselage and the installation of beams. The forward semi-fuselage will also undergo a trial fit of new air intakes. After completion, the assemblies will be sent for joining, and their places in the new stations will be taken by the semi-fuselages of the next MC-21 set.
* * *
In April, the media revisited the topic of the MC-21’s flight safety, particularly the combination of an expanded flight parameter monitoring system with an active side-stick control. Kirill Sypalo, Director General of TsAGI, noted that a distinctive feature of the MC-21 is the monitoring of over ten critical flight parameters, significantly surpassing the capabilities of previous-generation aircraft.
While the Tu-204 was limited to four motion parameters (g-load, angle of attack, Mach number, and speed), the MC-21’s limitations also include dynamic g-loads, critical angle of attack, flutter prevention, lateral stability, roll, and pitch.
The active side-stick provides tactile feedback to the pilot. Unlike the passive systems used in the Airbus A320 or the Chinese C919, the Russian development physically resists dangerous pilot inputs. As critical regimes are approached, the stick changes resistance or vibrates, warning the crew of potential hazards. Additional control system parameters include yaw control, prevention of excessive aileron or elevator deflections, automatic lateral channel balancing in the event of an engine failure, and engine operation monitoring to align with aerodynamic limitations. This multi-factor protection reduces the likelihood of crew error.
TsAGI believes that the MC-21’s safety system surpasses those used in previous-generation aircraft. Monitoring more parameters and the active side-stick provide a higher level of protection against emergencies.
* * *
The Ministry of Industry and Trade announced a tender for research and development work aimed at improving the competitiveness of the PD-14 engine. The R&D, designed to address several key tasks, is divided into three stages, with completion scheduled for December 2027.
Engineers will work to increase the engine’s lifespan, improve fuel efficiency, reduce weight, achieve additional noise reduction, and optimise production processes to decrease labour and material intensity in component manufacturing. The Ministry of Industry and Trade has allocated over 14 billion 230 million roubles (approx. $170 million) for this purpose. The PD-14 will also be refined based on the results of certification testing of the import-substituted aircraft version and the initial operational phase of the MC-21-310.
* * *
The company “Yakovlev” has commissioned an inflatable hangar for the line maintenance station at Kurumoch Airport (Samara). This hangar is the largest of its kind in Europe. It will be used for aircraft maintenance, including the short-haul “Superjet 100,” and in the future, the medium-haul MC-21-310. The first aircraft to undergo maintenance here will be an SSJ100 operated by Rossiya Airlines. The aircraft will undergo a 4Y-check (periodic maintenance).
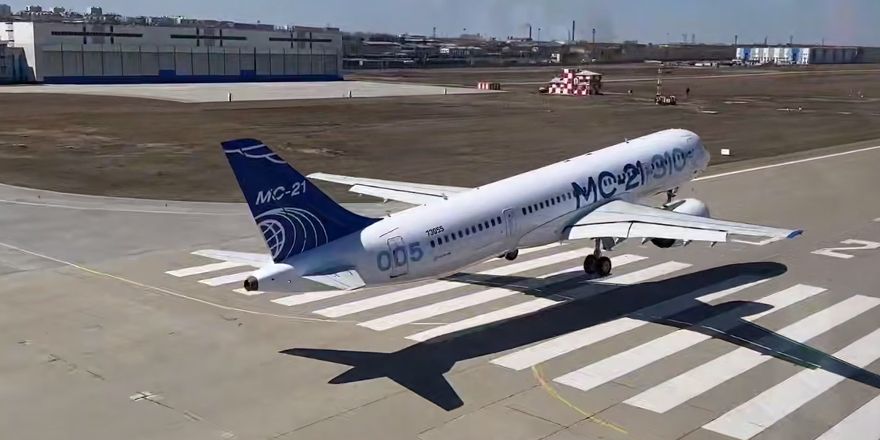
In mid-April, at a meeting of the Federation Council Committee on Economic Policy, Deputy Head of the Russian Ministry of Industry and Trade Gennady Abramenkov stated that the certification flights of the partially import-substituted MC-21 are expected to begin in spring 2025, with the fully Russified version following in summer. Work on finalising the aircraft’s configuration and ground testing of its systems is nearing completion. His words were confirmed by the first flight of aircraft 73055 (MS.0012) after replacing foreign systems on 29 April. Simultaneously, the installation of systems on aircraft 73057 (MS.0013), which is fully import-substituted, is being completed.
At the same time, preparations for serial production are underway. Twelve aircraft in various stages of readiness are assembled, awaiting the completion of certification testing and the installation of Russian systems. The completion of certification and the start of serial production of the MC-21 are key goals for the Russian aviation industry.
The prototype MC-21, tail number 73055, flew from Zhukovsky to Irkutsk on 7 July 2023. During modification, its inertial navigation system, auxiliary power unit, air conditioning and pressure regulation systems, lighting, and aircraft system panels were replaced with domestic versions. A Russian power distribution system and hydraulic system were installed. The landing gear was originally of Russian production. Partially imported components remain only in the avionics suite of this prototype.
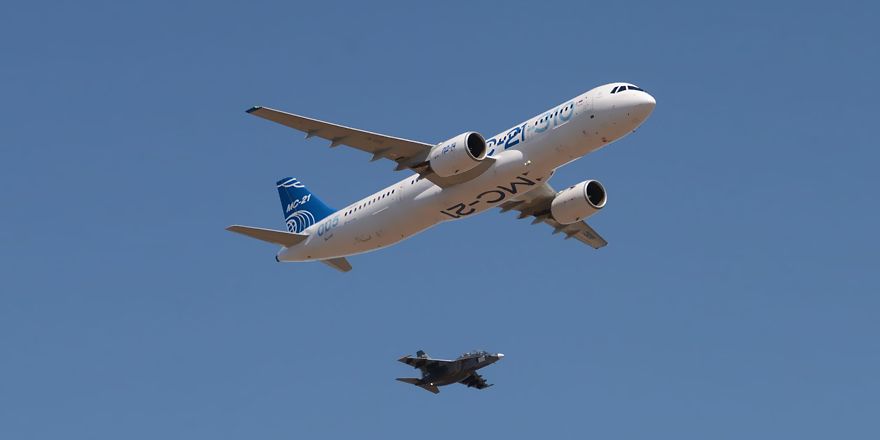
The most complex and labour-intensive task was replacing the electrical power system. French company Thales took seven years to develop a similar system for the MC-21-300. Russian engineers completed this task significantly faster. Now that the electrical power system has proven its functionality, work on integrating Russian components into prototype 73057 will be accelerated.
In May, 3-4 flights are planned as part of the refinement testing program, after which aircraft 73055 will fly to Zhukovsky for certification testing.
The first flight of aircraft 73055 lasted half an hour longer due to the need to yield to other aircraft landing at Irkutsk International Airport. Roman Taskaev reported this. Instead of the planned 50 minutes, the aircraft spent 80 minutes in the air. He noted that everything went according to plan, but the air traffic situation required yielding to aircraft approaching the civilian airport during landing.
According to Roman Taskaev, the aircraft confirmed the reliability of its systems in an unforeseen situation. This episode demonstrated the flexibility and adaptability of the MC-21’s control system. The crew accomplished their mission despite the changes to the first flight plan.
* * *
In Zhukovsky, the prototype MC-21-300 (tail number 73054) conducted three flights in April as part of certification testing to evaluate the performance of software components.