In 2023 the enterprises of the state corporation Rosatom doubled the volume of carbon fibre supplies for the Russian aviation industry, including for the production of composite wing of MS-21 medium-range aircrafts. This was reported in the press-service of the state corporation.
Also within the framework of the import substitution programme the deliveries of prepreg for the horizontal plumage of MS-21 are continued since 2023. In 2024 it is planned to start serial deliveries of prepreg for the narrow-body short-haul passenger aircraft SJ-100.
Carbon fibre is an innovative material for use in the aviation industry. It has high strength and stiffness at low density, which reduces the weight of the aircraft and improves its weight and aerodynamic performance. In addition, carbon fibre has good resistance to corrosion and other aggressive influences, which increases the service life of aircraft.
Currently, composite materials are used in the structures of various both foreign and domestic aircraft, including the A350, B787 and Superjet 100. Initially, Irkut chose foreign materials for the MS-21 project, as in the “noughties” Russia did not have the technology to create carbon fibre from polyacrylonitrile (PAN) precursors with filament strength characteristics at the T700-T800 level like foreign analogues. However, following the cessation of supplies of these materials in 2018, the need for proprietary technology has become vital.
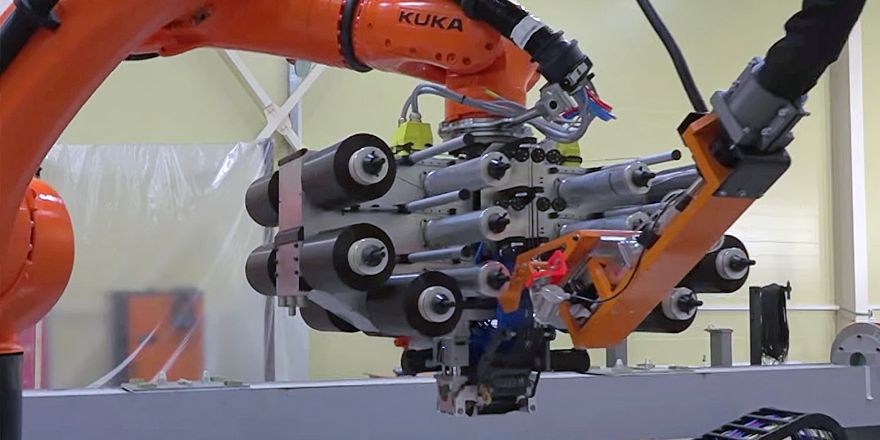
To date, Russian carbon fibres have a strength of 4.9 GPa, there are individual samples with a strength of 5.6 GPa and even 6 GPa, which is the same as Toho-Tenax or Cytec fibres – 6 GPa. However, in this field, strength is not the only or most important parameter. Therefore, even if we take into account only the fibres mass-produced in Russia, they are quite suitable for manufacturing large integrated structures of the first level: spars, wing panels and centre wing. The strength of domestic carbon fibre is reduced due to micro-roughnesses on its surface, but at the same time these micro-roughnesses improve the interaction with the polymer matrix and along with modification of the matrix and apprettes lead to improvement of the product performance characteristics.
Composites created from domestic carbon fibre are 15% stronger in compression and impact than composites made from Cytec materials, despite the fact that foreign fibres are stronger. This shows that Rosatom’s companies have successfully met the challenge of creating composites from domestic materials. In December 2023, the next stage of introducing domestic PCMs into the MS-21 design was completed.
During the year the technological testing of manufacturing of the aircraft power elements from Russian composite materials was carried out. Elementary samples of wing and centre wing caisson materials were tested to determine design characteristics. Together with TsAGI, the wing, centre wing, keel and stabiliser caissons, wing mechanisation and control surfaces, as well as static and repeated static tests of the pylon for the PD-14 engine mounting were tested. Repair technologies of composite units of MS-21 aircraft were also worked out.
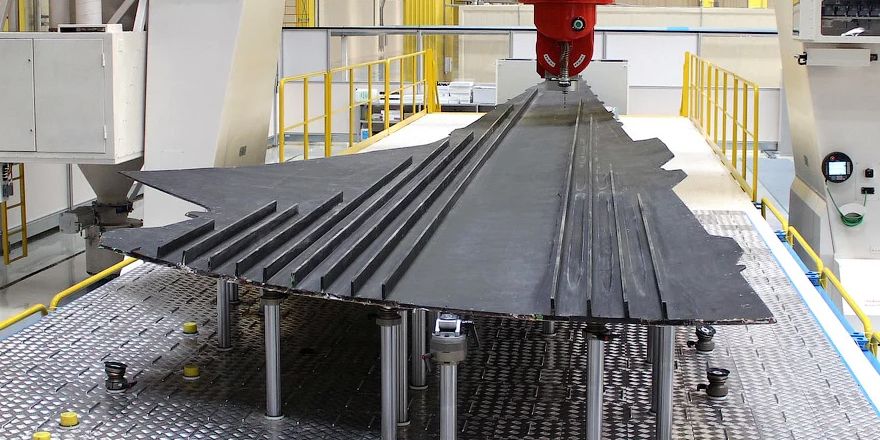
Ulyanovsk AeroComposite has been dealing with the issues of import substitution since 2015. By this time the production of the first wing consoles from imported materials has already been mastered, the technological process and the corresponding equipment have been worked out. The next stage was to switch to Russian PCMs. The work was organised with leading institutes, and by 2019 a prototype of the Russian material was ready, which made it possible to carry out its testing on full-size wing cantilever structures, perform general and special qualification of the new material, manufacture consoles for static and life tests and include the import-substituted material in the design documentation in the shortest possible time.
Now AeroComposite is dealing with the issues of import substitution of equipment. In 2020, R&D work was started with Platov South Russian University and MSTU named after Platov. Platov and Bauman Moscow State Technical University to create robotic complexes for laying out dry carbon ribbon. Now one prototype has been put into operation in the Moscow laboratory of AeroComposite, the second prototype is to arrive at the plant in Ulyanovsk in February and after its commissioning it will be involved in the main production programme. On the basis of technical solutions obtained in the course of manufacturing of prototypes of lay-out equipment, full-scale lay-out gantries and robots that will scale the production of cantilevers are being launched into production.
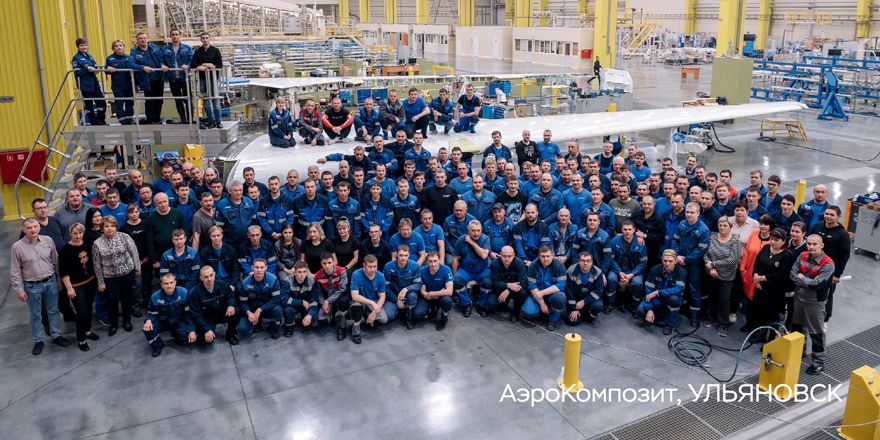
The existing production capacities of AeroComposite allow to manufacture up to 12 aircraft kits per year in Ulyanovsk. In order to increase the production volumes up to 36 MS-21 wing sets per year, the ToRs for manufacturing and delivery of Russian-made assembly station duplicates have already been developed. Currently, the MS-21 wing caisson is being assembled for the aircraft with serial number MS.0020. The technological cycle of manufacturing of one wing bracket provides that the wing can stay at the final panel installation station for up to 4 weeks. At the wing tail and nose section assembly station, the work also takes about 4 weeks, and at the airframe assembly station – about 10 days.
In 2023, AeroComposite produced two prototypes of the wing caisson under the long-range wide-body programme. Now the products are undergoing static and resource tests. This work has given the enterprise confidence that with the current technologies it is not difficult to produce a composite wing for a wide-body long-haul aircraft, which can be both the Chinese C929 and the future project, the prototype for which can be the Il-96-400M airliner.