Modern unmanned aerial vehicles use open propellers as a propulsion and lifting device. This design is actually typical for both civilian drones and FPV and reconnaissance and strike drones, which are massively used in the area of special military operation. The open propeller is characterised by low cost, it is easy to manufacture and maintain, compact, and the composite blades are easy to replace in case of damage.
At first glance, a four-, six- or eight-beam drone seems very simple: an electric motor and two-blade propellers, sometimes coaxial on each beam. But the design solutions known today are far from ideal, and above all, this is due to the peculiarities of each of the nodes. An electric motor has maximum torque at low rotor speeds. As the flight speed increases, the torque decreases, and in most operating modes the electric motor power is excessive, which affects the mass of the final product. Moreover, increasing the number of blades of an open propeller does not improve its efficiency, and the most common remain two-bladed propellers.
Achieving speeds over 300 km/h on quadrocopters using open propellers is practically impossible due to design limitations and inexpedient due to noise at take-off modes, vulnerability to contact with external objects.
The most promising solution for high-speed electric unmanned aircraft systems is a cowled fan, whose casing prevents debris from flying sideways in case of an accident and poses less danger to passengers, structural elements and valuable cargo. In addition, the engine cowling can create additional lifting force, compensating for the frontal resistance to the oncoming air flow, and the outgoing flow has practically no residual twist due to the installation of a straightening apparatus, which has a positive effect on the efficiency of the propulsion system and reduces the noise of the UAV.
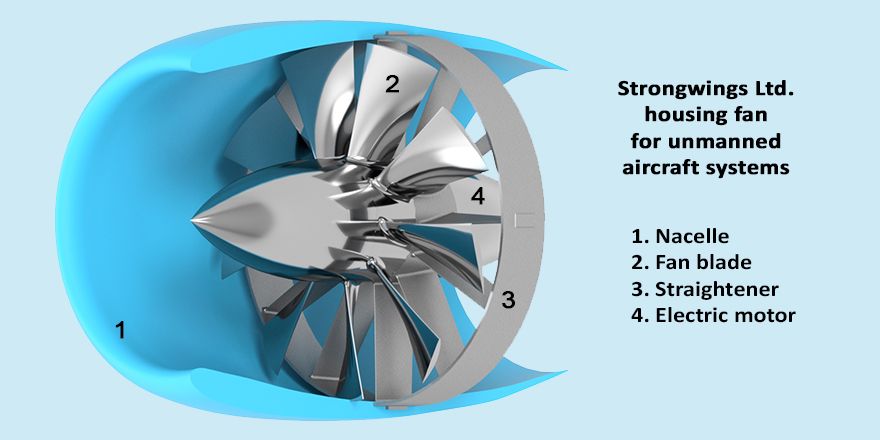
Engineers from Strongwings (Ekaterinburg) have developed a similar electrically driven fan with increased efficiency and reduced noise levels, which was made possible through the use of special geometry fan blades that ensure a smooth flow of airflow inside the housing.
“Today, open propellers are most commonly used on small aircraft and drones. However, the use of such propellers creates a high level of noise, due to which the devices cannot be used in urban conditions,” the company said. – Strongwings is developing electric drive motors for use in small aircraft, including unmanned aircraft. Such motors reduce the noise level from aircraft operation and increase the safety of their operation. They also extend the range of horizontal flight speeds.”
According to project manager (https://aviation21.ru/v-rossii-sozdany-marshevye-kapotirovannye-elektroprivodnye-ventilyatory-dlya-maloj-aviacii/) Igor Tetkin, the company has already created a sample of the bonneted electric motor and a stand for its testing. These propulsion systems are expected to appear on the market by the end of this year upon completion of tests as part of UAVs. The development of Russian engineers can find application in vertical take-off and landing aircraft (UAVs, eVTOL), in aircraft-type UAS, fixed wing systems and in multi-rotor designs.
“We plan to produce electric drive motors for various types of small aircraft including drones, helicopters and amphibious aircraft. The motors can also be used as auxiliary propulsion systems on large aircraft,” Strongwings added.