On 2 December 2023 AeroComposite Joint Stock Company celebrated its fifteenth anniversary. The enterprise was created as a specialised competence centre for composite solutions for aviation, and in particular for the MC-21 aircraft. Now the company consists of three enterprises: the experimental laboratory of technologies and constructions from PCM in Moscow, Ulyanovsk plant AeroComposite and Kazan plant KAPO-Composite.
In the process of recovery and development of the aviation industry after the collapse in the 90s, our country needed to organise the production of new-generation civil aircraft to compete with Western models and interest carriers in Russian equipment. In an interview in 2016, Oleg Demchenko (then President of Irkut Corporation and General Designer of the Yakovlev Design Bureau) recalled that during the development of the MC-21 aircraft, he invited many leading specialists of the Russian aircraft industry, including Genrikh Novozhilov, for consultations. As a result, they agreed that the wing should be composite.
Manufacturing of composite parts in the aircraft industry is a complex technological process, one of which is autoclave moulding based on the use of prepregs – composite materials-semifinished products consisting of carbon fabrics impregnated with polymer resin. The advantage of this method is that it does not require specialised equipment for prepreg moulding, but some disadvantages of the technology do not allow to create one-piece large-size power elements of aircraft structure and affect the cost of parts production. First of all, the duration of the moulding process and the limited shelf life of prepregs are the factors that determine the price of the final product. According to regulatory documents, the warranty period of prepregs storage in a freezer is 12 months at temperatures from -19°C to -17°C. In addition, the part blank can be used at the production site only within 10 days at a temperature of 20±2°C.
An alternative to autoclave moulding technology is “direct” processes, which combine the operations of impregnation of carbon fibre with polymer resin and moulding of the part. This allows to shorten the production cycle time, reduce energy and labour costs, as well as reduce the cost of manufacturing structures. But most importantly, if prepregs and autoclaves are not used, the size of manufactured parts, such as wing spars and panels, can be increased.
One of the methods of non-autoclave moulding is Vacuum Assisted Resin Transfer Moulding (VARTM). This process is based on impregnation of dry carbon fibre and moulding of the part using a vacuum bag attached to the tooling. The polymer resin penetrates the mould due to the vacuum generated under the vacuum bag. The VARTM method significantly reduces the cost of pre-production of large structures, as simpler and cheaper tooling is required.
But vacuum infusion technology has disadvantages and the most significant one is the difficulty in reproducibility of the process. Dry carbon tape will shift when laid out on the tooling, and a method is required that will allow the fibre layers to be bonded to each other without the use of a binder – a polymer resin. The equipment, materials and the lay-up process itself has never been used before in the aircraft industry.
On the 2nd of December 2008 AeroComposite CJSC was established for the purpose of implementation of vacuum infusion method for manufacturing of all-composite wing of MC-21 aircraft. The enterprise had a task to form a research platform for testing of applied materials and working out of technologies for production of power composite structures for aviation. It was also required to create production centres – factories for production of aviation purpose units from PCM. Anatoly Gaidansky was appointed the General Director of AeroComposite.
The technological level of carbon fibre production in Russia at the moment of the beginning of work on the MC-21 aircraft was lower than in the West. The tensile strength of carbon fibre on the basis of polyacrylonitrile (PAN) precursors with the characteristics of Toray’s T800S yarns, which is used for the production of the first level parts for Boeing 787, is 5880 MPa, while the Russian one is 3500 MPa. This value is roughly on par with Toray’s T300 material, which was developed in the 1970s. After the collapse of the USSR, Russia was not up to developing technologies, so it was considered to be lagging behind the West in carbon fibre production.
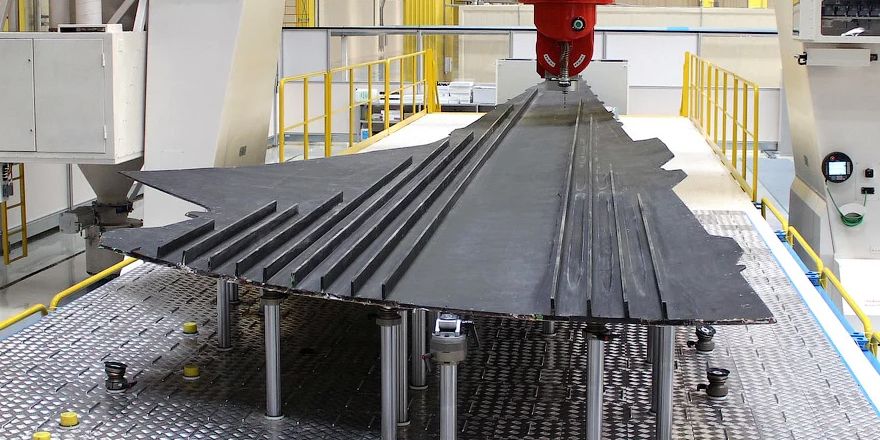
From 2009 to 2012, AeroComposite liaised with foreign companies around the world to select materials and equipment for a repeatable process of the required precision and quality. Initially it worked with the American company Hexcel, but later AeroComposite switched to alternative suppliers. The products of Belgian Solvay, whose American division Cytec Industries produces both resins and dry carbon fibre, as well as Japanese company Toho-Tenax, which produces carbon filaments, were chosen.
The technology of production of power structures of the first level of “black” wing of MC-21 aircraft was created by the specialists of AeroComposite, technological equipment was developed together with foreign manufacturers. Robotic units for dry automated lay-up of carbon fibre for the production of wing spars were supplied by Coriolis Composites. A robotic machine that lays out the tape for wing panels was supplied by Spain’s MTorres. The TIAC thermal infusion centres were developed by French company Stevik.
In 2018, after the introduction of another package of sanctions against the Russian aircraft industry, and in particular against Irkut and AeroComposite, the question of forcing the development of domestic carbon tape of the required strength arose. This task was solved by Rosatom Corporation in the shortest possible time – already in December 2021 MC-21 with a wing made of Russian composites took to the sky. But it was only the beginning, it was necessary to create the technological equipment for dry fibre laying out.
In September 2022 the Federal Service for Intellectual Property issued to the Prepreg – Modern Composite Materials Joint Stock Company the patent RU 2779663 C1 for polymer shrink additive as a binder layer. The additive binder is placed between layers of dry carbon fibre and is melted by the laser of the laying head, providing gluing of layers. In the process of vacuum infusion under the influence of high temperature of polymer resin – binder, the binder is dissolved.
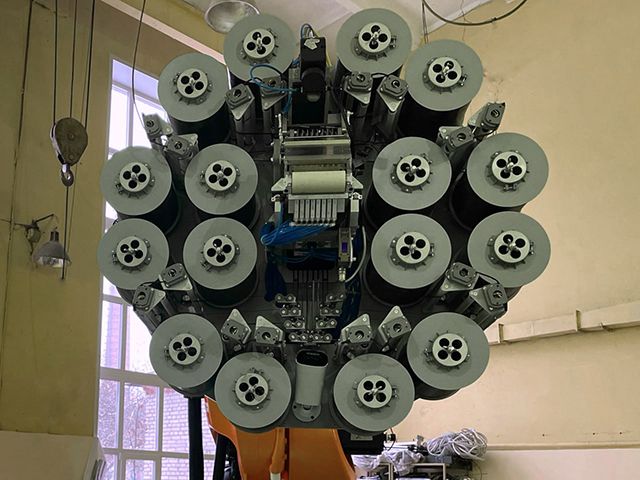
The lay-out required the creation of robotic manipulators for the production of spars and wing panels with integrated stringers. Such equipment is highly specialised and there is no mass production of it in the world. “AeroComposite” attracted foreign companies to develop such equipment, but after the imposition of sanctions, the partnership was broken. It was necessary to create such robotised complexes ourselves, and they have already been created.
Stacking robots for automating the process of laying out dry carbon ribbon were developed by joint efforts of PJSC Yakovlev, AeroComposite, Bauman Moscow State Technical University and Platov South Russian State Polytechnic University. Samples of lay-out mechanisms are undergoing pilot operation in the Moscow laboratory of AeroComposite and in the Moscow Region branch of MSTU in Dmitrov. Serial samples of the Russian robotised complex will soon be sent to Ulyanovsk, to the company’s production site.
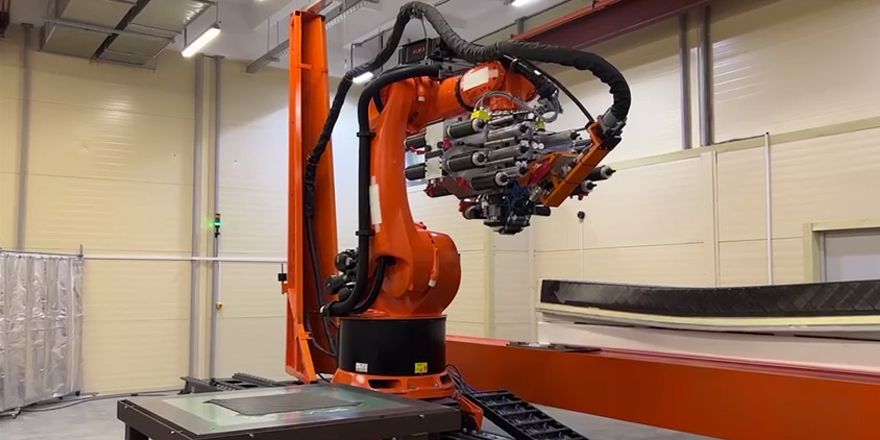
For 15 years in Russia the industry of modern high-tech polymer-composite materials has been created practically from scratch. The technology of manufacturing power large-size wing structures from PCM has been developed, which provides one of the competitive advantages of MC-21 aircraft – composite wing with improved aerodynamic characteristics. A scientific and technical reserve for future projects has been created, in particular, strength tests of the wing caisson of a promising wide-body long-haul C929 aircraft being developed by COMAC are underway at TsAGI.
The Ulyanovsk plant AeroComposite specialises in the production of wing spars and panels with stringers, as well as the centre wing for MC-21 by vacuum infusion. The Kazan enterprise “KAPO-Composite” produces composite units of wing mechanisation, plumage, elements of nose and tail parts of MC-21 wing. Here the method of autoclave moulding on the basis of prepregs is applied.
In close cooperation between PJSC Yakovlev and AeroComposite and the leading universities of the country, robotic complexes for automatic lay-out of dry carbon ribbon have been created. The key elements of the robots, including software and the lay-out head, are designed and manufactured in Russia.